athrough Kaizen or Continuous Improvement We Address Customer NeedsaÂ
What is Kaizen?
Kaizen is an approach to creating continuous improvement based on the idea that small, ongoing positive changes can reap significant improvements. Typically, it is based on cooperation and commitment and stands in contrast to approaches that use radical or top-down changes to achieve transformation. Kaizen is core to lean manufacturing and the Toyota Way. It was developed in the manufacturing sector to lower defects, eliminate waste, boost productivity, encourage worker purpose and accountability and promote innovation.
As a broad concept that carries myriad interpretations, it has been adopted in many other industries, including healthcare. It can be applied to any area of business and even on the individual level. Kaizen can use a number of approaches and tools, such as value stream mapping -- which documents, analyzes and improves information or material flows required to produce a product or service -- and Total Quality Management -- which is a management framework that enlists workers at all levels to focus on quality improvements. Regardless of methodology, in an organizational setting, the successful use of Kaizen rests on gaining support for the approach across the organization and from the CEO down.
Kaizen is a compound of two Japanese words that together translate as "good change" or "improvement." However, Kaizen has come to mean "continuous improvement" through its association with lean methodology and principles.
Kaizen has its origins in post-World War II Japanese quality circles. These circles or groups of workers focused on preventing defects at Toyota. They were developed partly in response to American management and productivity consultants who visited the country, especially W. Edwards Deming, who argued that quality control should be put more directly in the hands of line workers. Kaizen was brought to the West and popularized by Masaaki Imai via his book Kaizen: The Key to Japan's Competitive Success in 1986.
10 principles of Kaizen
Because executing Kaizen requires enabling the right mindset throughout a company, 10 principles that address the Kaizen mindset are commonly referenced as core to the philosophy. They are:
- Let go of assumptions.
- Be proactive about solving problems.
- Don't accept the status quo.
- Let go of perfectionism and take an attitude of iterative, adaptive change.
- Look for solutions as you find mistakes.
- Create an environment in which everyone feels empowered to contribute.
- Don't accept the obvious issue; instead, ask "why" five times to get to the root cause.
- Cull information and opinions from multiple people.
- Use creativity to find low-cost, small improvements.
- Never stop improving.
How Kaizen works
Kaizen is based on the belief that everything can be improved, and nothing is the status quo. It also rests on a Respect for People principle. Kaizen involves identifying issues and opportunities, creating solutions and rolling them out -- and then cycling through the process again for inadequately addressed issues and problems. A cycle made up of seven steps can be implemented for continuous improvement and can provide a systematic method for executing this process.
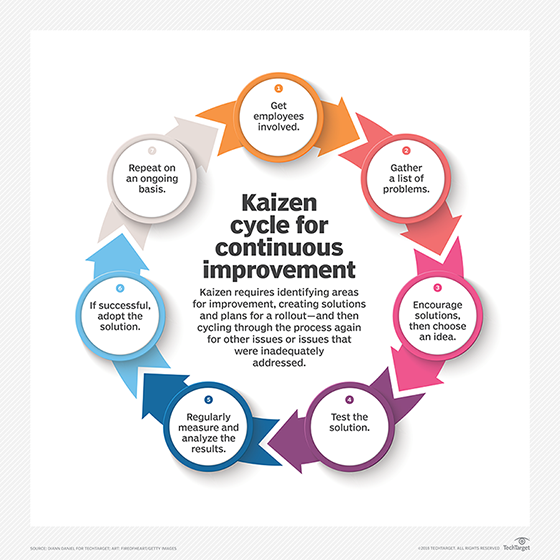
Kaizen cycle for continuous improvement
Kaizen can be implemented in a seven-step cycle to create an environment based on continuous improvement. This systematic method includes the following steps:
- Get employees involved. Seek the involvement of employees, including soliciting their help in identifying issues and problems. Doing so creates buy-in for change. Often, this is organized as specific groups of individuals charged with gathering and relaying information from a wider group of employees.
- Find problems. Using widespread feedback from all employees, gather a list of problems and potential opportunities. Create a list if there are many issues.
- Create a solution. Encourage employees to offer creative solutions, with all manner of ideas encouraged. Pick a winning solution or solutions from the ideas presented.
- Test the solution. Implement the winning solution chosen above, with everyone participating in the rollout. Create pilot programs or take other small steps to test out the solution.
- Analyze the results. At various intervals, check progress, with specific plans for who will be the point of contact and how best to keep ground-level workers engaged. Determine how successful the change has been.
- If results are positive, adopt the solution throughout the organization.
- These seven steps should be repeated on an ongoing basis, with new solutions tested where appropriate or new lists of problems tackled.
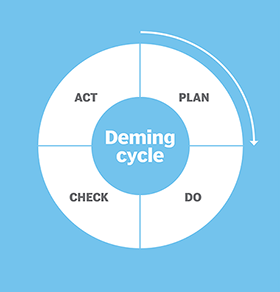
Additional approaches to the Kaizen cycle exist, such as one that is condensed into four steps -- plan, do, check, act, or PDCA. It is also known as the Shewhart cycle or Deming cycle.
Types of Kaizen events
Although the aim of Kaizen is widespread cultural change, the events to kick-start the efforts involved or focus on a specific set of problems have evolved.
In the West, these concentrated efforts to make quick changes to achieve a short-term goal are often the extent of Kaizen efforts. There are numerous names associated with Kaizen events, including Kaizen blitz, Kaizen burst, Kaizen workshop, focused improvement workshop, continuous improvement workshop and rapid process workshop. These events can rely on various tools or focus on specific areas, such as the 5S framework, total productive maintenance and value stream mapping.
Kaizen 5S framework
A 5S framework is a critical part of the Kaizen system and establishes an ideal physical workplace. The 5Ses focus on creating visual order, organization, cleanliness and standardization to improve profitability, efficiency, service and safety. Below are the original Japanese 5Ses and their common English translations.
- Seiri/Sort (organize). Separate necessary workplace items from unnecessary ones and remove unnecessary items.
- Seiton/Set in order (create orderliness). Arrange items to allow for easy access in the way that makes the most sense for work.
- Seiso/Shine (cleanliness). Keep the workspace clean and tidy.
- Seiketsu/Standardize (standardized cleaning). Systematize workplace cleanup best practices.
- Shitsuke/Sustain (discipline). Keep the effort going.
Advantages and disadvantages of Kaizen
There are several reasons why Kaizen can be an advantage for an organization; however, there are some situations for which it is less suited. Some of Kaizen's advantages and disadvantages include the following:
Kaizen advantages
- Kaizen's focus on gradual improvement can create a gentler approach to change in contrast to big efforts that may be abandoned due to their tendency to provoke change resistance and pushback.
- Kaizen encourages scrutiny of processes so that mistakes and waste are reduced.
- With fewer errors, oversight and inspection needs are minimized.
- Employee morale improves because Kaizen encourages a sense of value and purpose.
- Teamwork increases as employees think beyond the specific issues of their department.
- Client focus expands as employees become more aware of customer requirements.
- Systems are in place to ensure improvements are encouraged both in the short and long terms.
Kaizen disadvantages
- Companies with cultures of territorialism and closed communication may first need to focus on cultural changes to create a receptive environment.
- Short-term Kaizen events may create a burst of excitement that is shallow and short-lived and, therefore, is not sustained.
Examples of Kaizen
Toyota is arguably the most famous for its use of Kaizen, but other companies have successfully used the approach. Here are three examples:
- Lockheed Martin. The aerospace company is a well-known proponent of Kaizen. It has used the method to successfully reduce manufacturing costs, inventory and delivery time.
- Ford Motor Company. When lean devotee Alan Mulally became CEO of Ford in 2006, the automaker was on the brink of bankruptcy. Mulally used Kaizen to execute one of the most famous corporate turnarounds in history.
- Pixar Animation Studios. Pixar applied the continuous improvement model to reduce the risks of expensive movie failure by using quality control checks and iterative processes.
This was last updated in May 2021
Continue Reading About Kaizen (continuous improvement)
- Define a continuous improvement process with EA models, practices
- Production leveling helps eliminate waste
- Continuous improvement teams enable transformation
- Traditional accounting gets lean
- Words to go: ITSM methodologies for enterprises
Dig Deeper on Supply chain and manufacturing
-
iPhone
-
business process improvement (BPI)
-
poka-yoke
-
project management framework
Source: https://www.techtarget.com/searcherp/definition/kaizen-or-continuous-improvement
0 Response to "athrough Kaizen or Continuous Improvement We Address Customer NeedsaÂ"
Enregistrer un commentaire